Contatto Editoriale:
Paolo Lista,
Lista Studio srl®
Borgo Belvigo 33, 36016 Thiene Vi ITALY
tel/fax 0445,372479 o info@lista.it
La realizzazione di un sistema di automazione industriale
richiede ancora oggi la considerazione dell'inevitabile
richiesta di un intervento diretto dell'uomo, anche se
occasionale, per interventi di manutenzione.
Recentemente la Plasma-Therm Inc. di St. Petersburg,
in Florida (USA), ha esteso la sua linea di produzione
con un mescolatore robotizzato per la deposizione del plasma
e dei prodotti di supporto, chiamato Versalock.
I macchinari della Plasma-Therm devono operare in ambienti
estremamente puliti, usando camere a vuoto per cuocere al forno
materiali a base di silicio per pannelli per computers, testine
di lettura e scrittura e altri prodotti ad alta tecnologia.
L'accesso al robot di caricamento automatico e alla camera
per la mescola del plasma si trova attraverso un piccolo quanto pesante
coperchio, attraverso il quale bisogna mantenere il vuoto.
Questo coperchio, dal peso di quasi 50 kg, doveva tuttavia essere agevolmente
apribile da una sola persona quando il mescolatore robotizzato
presentava necessità di interventi di manutenzione.
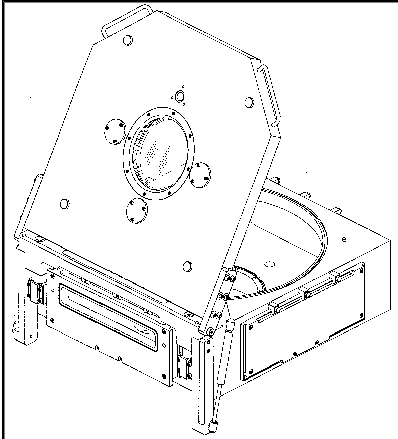
La direzione della Plasma-Therm
aveva imposto l'uso di ammortizzatori anzichè di servomotori
sul coperchio per ridurre il costo totale di produzione
del nuovo Versalock.
La sfida tecnologica non era affatto elementare, non essendo facile
determinare il dimensionamento degli ammortizzatori per consentire
la facile apertura del coperchio da un lato ed il loro corretto
inserimento nelle dimensioni fisiche così contenute del Versalock.
A complicare le cose si aggiungevano vari vincoli esterni che
riducevano ulteriormente lo spazio a disposizione per gli ammortizzatori,
primo tra tutti lo spazio operativo dell'alimentatore esterno
verticale del silicio da trattare.
Di norma, un ingegnere della Plasma-Therm con una notevole
preparazione fisica avrebbe dovuto procedere comunque
per tentativi, con complesse equazioni da risolvere, per
trovare la forza necessaria per gli ammortizzatori. Successivamente,
il ricorso a vari prototipi fisici sarebbe stato inevitabile per
determinare la posizione in cui questi ammortizzatori sarebbero stati
più efficaci. Al contrario è bastato affidare il problema ad un
giovane progettista, senza particolare preparazione nel settore,
per ottenere da questo la soluzione del problema in soli tre giorni
grazie al ricorso ad un software di analisi cinematica e dinamica.
Jeff Barriault - progettista meccanico alla Plasma-Therm - è ricorso
al Working Model della Knowledge Revolution (San Mateo, California, USA)
per risolvere il suo incarico.
Il Working Model è un programma di analisi cinematica e dinamica
che applica le leggi della fisica ai modelli CAD.
Barriault iniziò a sviluppare la soluzione fornito solo di una copia del
software e dei vincoli dimensionali.
Dopo aver schizzato le dimensioni del Versalock in AutoCAD, Barriault
ricorse al catalogo di un produttore di ammortizzatori per inserire questi
elementi nel suo progetto. Importò poi il suo design preliminare da AutoCAD
nel Working Model tramite il formato DXF. Barriault aggiunse
alcuni vincoli al modello in modo che il suo ammortizzatore
"virtuale" operasse come nella realtà; in altre parole, in modo che
questo esercitasse un'azione crescente con la corsa di caricamento.
"Ho copiato la formula riportata dal costruttore nel catalogo
degli ammortizzatori e l'ho inserita in una delle finestre di dialogo del
Working Model; ho riprodotto così proprio il comportamento reale di
quell'ammortizzatore ed ho poi aggiunto i finecorsa di estensione e
compressione."
Questi vincoli si aggiungono in modo intuitivo e rapidissimo, basta un click
del mouse sui menù a tendina del Working Model; si apre subito una finestra di
dialogo dove l'utilizzatore può inserire delle proprie formule o accettare
quelle standard automaticamente proposte dal software con esame intelligente
delle dimensioni, masse e forze in gioco.
Dopo aver inserito un vincolo tipo corda ed un separatore nel pattino
dell'ammortizzatore, Barriault cliccò sul pulsante
"Run" per esaminare la risposta dell'ammortizzatore all'applicazione
di uno sforzo di apertura sulla maniglia del coperchio.
Per trovare la migliore posizione per l'ammortizzatore si è poi proceduto per
tentativi sul prototipo "virtuale" così realizzato, bloccando prima
un'estremità e spostando l'altra in una nuova posizione per vedere come
variava lo sforzo di apertura. (Barriault aveva pensato in effetti di usare
due ammortizzatori, ma dal momento che ne aveva modellato uno solo bastava
tener conto del doppio dei risultati ottenuti.)
"Al punto di fulcro ho inserito un motore a velocità costante,"
ha spiegato Barriault. "Quando il coperchio si trovava ad una certa angolazione
potevo vedere la coppia istantanea necessaria a mantenerlo aperto
tramite l'apposita finestra di misura del Working Model."
Barriault continuò a provare nuove posizioni per l'ammortizzatore
trovando infine quella ottimale in cui con una forza di poco più di 3 kg
si poteva aprire il coperchio e con 4,5 kg si riusciva a chiuderlo.
"Niente male per un coperchio da quasi 50 kg," aggiunse.
Un giovane assistente suggerì che Barrault rifinisse
il suo progetto simulando l'usura dell'ammortizzatore, per considerare cioè
quale forza sarebbe stata necessaria dopo mesi e mesi di uso continuativo.
Per sicurezza si sarebbe inoltre dovuto tenere un margine di circa il 10%.
Barriault reinserì l'equazione della forza nel Working Model
con un coefficiente legato ai cicli di lavoro per tener conto dell'usura.
Eseguì poi un nuovo ciclo di simulazioni, usando la stessa posizione ottimale per
gli ammortizzatori, ma con una forza inferiore del 10% per provare in sicurezza se comunque
il coperchio fosse tenuto fermo nella posizione di apertura.
Ed in effetti questo fu proprio il risultato ottenuto.
Se egli avesse dovuto eseguire tutte queste simulazioni con calcoli manuali,
di certo non avrebbe prodotto alcun risultato utile, non avendo
sufficiente preparazione matematica e tempo a disposizione per risolvere
i complessi sistemi di equazioni che descrivevano il sistema.
Il direttore del reparto progettazione, anch'egli ingegnere, rimase impressionato
dall'abilità di Barriault nel risolvere in tempo così breve
il progetto richiesto tramite il Working Model. Un pò incredulo,
volle eseguire lui stesso manualmente i calcoli matematici necessari
per controllare i risultati ottenuti, anche se questo era possibile solo per
qualche particolare posizione e a costo di impiegare tutto il tempo necessario.
I risultati erano identici.
"Sarebbe stato molto più oneroso progettare il Versalock senza il
Working Model," ha concluso Barriault,
"probabilmente dopo settimane di duro lavoro." Invece,
il nuovo modello è in produzione solo dopo pochi giorni di progettazione.
La Plasma-Therm, grazie alla prototipazione virtuale con il Working Model
è ora in grado di condurre a conclusione tutti i progetti di nuovi prodotti
con risultati positivi e documentati in tempi rapidi, con evidenti economie
di tempo e di risorse materiali. L'uso delle nuove versioni bidimensionale
e tridimensionale del Working Model, autosufficienti o integrate rispettivamente in AutoCAD e Mechanical Desktop,
ha inoltre consentito di annullare i tempi di importazione delle geometrie
e dei modelli solidi, consentendo la completa simulazione cinematica e dinamica in modo
trasparente all'interno dello stesso CAD.