Contatto Editoriale:
Paolo Lista,
Lista Studio srl®
Borgo Belvigo 33, 36016 Thiene Vi ITALY
tel/fax 0445,372479 o info@lista.it
A Washington forestry equipment manufacturer makes labor-saving machine possible with SolidWorks '97 and Working Model 3D software
Tinino, Washington, USA - Imagine a single machine that could
revolutionize forestry by cutting and felling a tree, stripping its limbs,
and placing it on a truck for shipping in minutes.
This unlikely device, called a cut, fall and load (CFL) grapple, wasn't
lifted from the pages of a logger's fantasy. It is becoming reality
in the Washington headquarters of forestry equipment manufacturer
Danzco with the help of SolidWorks and partner software from Working Model,
Inc.
Danzco's cut, fall and load system, which was presented at the Pacific
Logging Congress' outdoor show on September 18, 1997, is a forest industry
first.
quot;We've wanted to put together a CFL system for a long
time," says Ed Danzer of Danzco.
"But until we had a
software solution that enabled us to reduce weight significantly
in the design stage, CFLs were doomed to be too heavy for practical
use."
How to Design Fast and Light
To make the first-ever CFL light enough to move around the forest
floor and durable enough to survive an rugged logging environment
required Danzco to consider every conceivable weight saving measure
and calculate its effect on durability.
"It's like developing a high performance fighter plane that can
take a lot of shots too," explains Danzer.
"But that takes a lot of calculations and innovative engineering
throughout the machine."
Danzco also needed to engineer high quality into the CFL to minimize
warranty costs over the course of the CFL's product life.
"Our CFL line will probably sell about 400-500 units in its
first four years," says Danzer.
"With those kind of numbers we can't amortize warranty costs
over a large volume. The product has to be as close to perfect as
possible when it leaves the factory."
Because money and time constraints prohibited Danzco from using
a physical prototype for design tests, Danzco required a design
and analysis software solution that could accurately capture
design revisions, calculate the effects of material configurations
on weight and performance, and simulate the CFL's functions in reaction
to numerous design iterations.
That feat was accomplished with a
solution mating SolidWorks '97 3D CAD with Working Model 3D v2.0 motion
analysis software from Working Model Inc., and COSMOS/Works for finite
element analysis.
Desktop Creation
Danzer created the basic geometry and solid models of the CFL in
SolidWorks '97.
As a long-time user of SolidWorks, Danzer was thrilled
by the improved user friendliness and stability of the software,
noting that SolidWorks '97 enables him to be more productive because
he can spend more time engineering and creating than learning the
software's functions or dealing with system performance.
"The greatest software in the world isn't worth anything to me
if it's hard to use and hard to learn," says Danzer.
"Solid Works and Working Model don't have steep learning curves
and are very stable.
We consider our design software to be tools,
and if we had to spend more time learning how to use our tools rather
than applying them, our operational costs would skyrocket."
SolidWorks and Working Model also save Danzco money by providing
an affordable foundation for their design solution.
"As a Windows-based software, SolidWorks and Working Model
enable us to use common desktop hardware we can afford.
Five years ago,
we could not have undertaken the designs and analysis we do on computers
because we could not afford the hardware and software.
SolidWorks and Working Model are amazingly capable products for the price.
You get a lot of bang for the buck and we save a ton on development
and operational costs," states Danzer.
Communicating the Complex, Imagining the Impossible
Danzco also takes advantage of the improved design communication
that both SolidWorks '97 and Working Model 3D make possible.
"With SolidWorks we can communicate designs to a customer in a way
we never could before.
When you can show a customer how a project
will turn out in its earliest stages, you're more likely to get the
approval that moves a project along faster. With Working Model we can
easily bring in SolidWorks geometry after a design revision and actually
watch it work. If a design fails we can tell exactly what the cause is,
revise the design in SolidWorks, and check it again in Working Model.
I'm always amazed by how easy it is."
Along with finite element analysis software, SolidWorks '97 and
Working Model 3D are enabling Danzco to consider design possibilities
at a greater rate than ever before, meaning faster design cycles.
But SolidWorks '97 and Working Model 3D also help eliminate the materials
waste that accompanies destructive testing of prototypes.
As Danzer explains, "Before Working Model, an engineer made a lot of
educated guesses about whether a design would work. Sometimes those
guesses are wrong, but when you're working on the prototype of a limited
production item like a CFL, you can't afford to guess wrong.
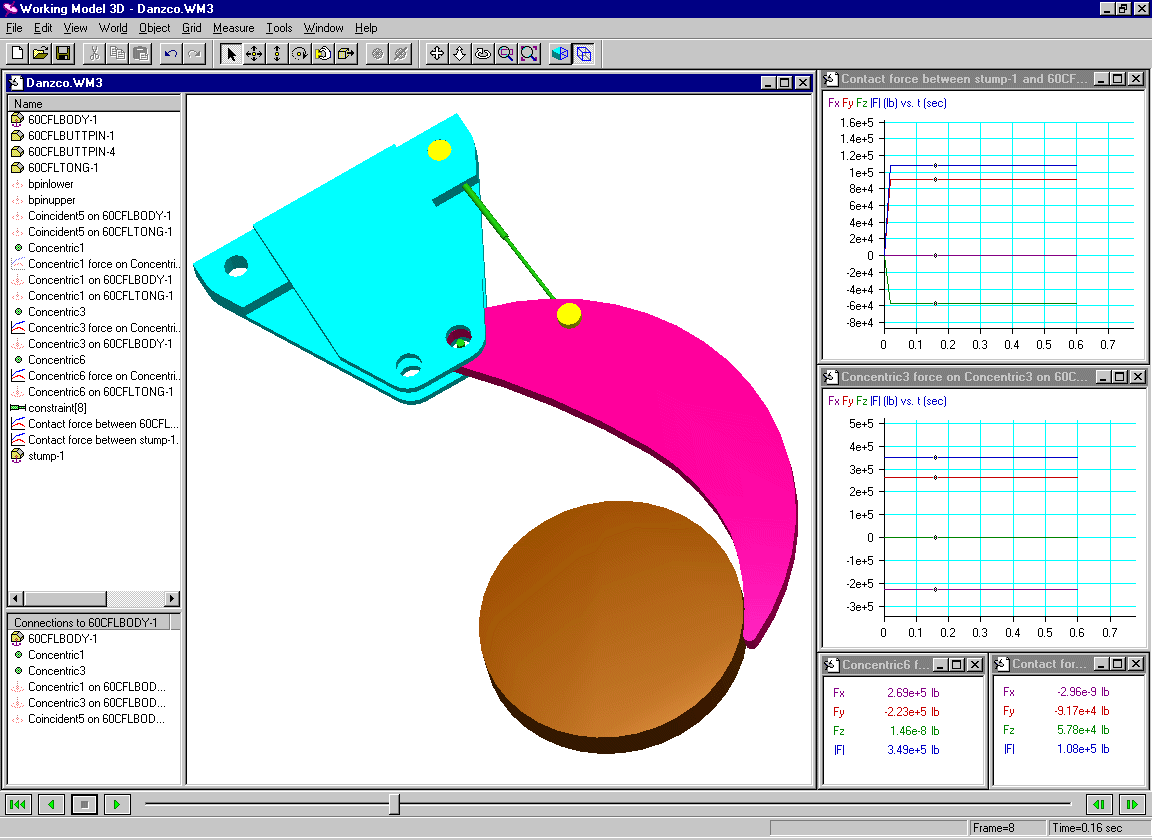
Click here
to download the VRML file of a forestry equipment in action.
Please read the instructions on VRML before..
With Working Model we can do a thorough analysis of a mechanism without
blowing anything up.
We can consider designs we never would on
a physical prototype."
Though SolidWorks and Working Model have helped Danzco achieve
enormous savings in time and resources, the software has also lent
a more important luxury to Danzer and his team of engineers;
the time and flexibility to imagine and consider the impossible.
"The greatest benefit of using SolidWorks and Working Model
is that we have the ability to do things we've never done before,"
explains an excited Danzer.
"We're opening markets that never
existed and for now we're all alone on top.
That's a nice place to be."