Contatto Editoriale:
Paolo Lista,
Lista Studio srl®
Borgo Belvigo 33, 36016 Thiene Vi ITALY
tel/fax 0445,372479 o info@lista.it
PNEUMATIC LOADER VIRTUAL PROTOTYPE AND SIMULATION
Cliccare qui per il testo in italiano
An example of cinematic and dynamical simulation, performed with visualNastran 4D and Matlab/Simulink, applied to an industrial pneumatic loader, described as a result of the efforts of a team of graduating student (Giulio Di Gravio, Francesco Costantino and Andrea Cherubini) of Prof. De Carli at Rome "La Sapienza" University in Italy
During the Industrial Automation course of the faculty of Mechanical Engineering at the University “La Sapienza” of Rome, led by Prof. Alessandro De Carli, the students, as an integrant part of the final exam, were invited to present a team work dealing with the application to a real industrial case of the control and simulation techniques developed during the lectures.
Our analysis concerns a common model of pneumatic loader that Topfloor Sud s.r.l. uses in its firm in Carsoli (AQ) to move wood or inert material panels (dimensions 600x600mm, thickness 30mm), intended to the production of raised access floors.
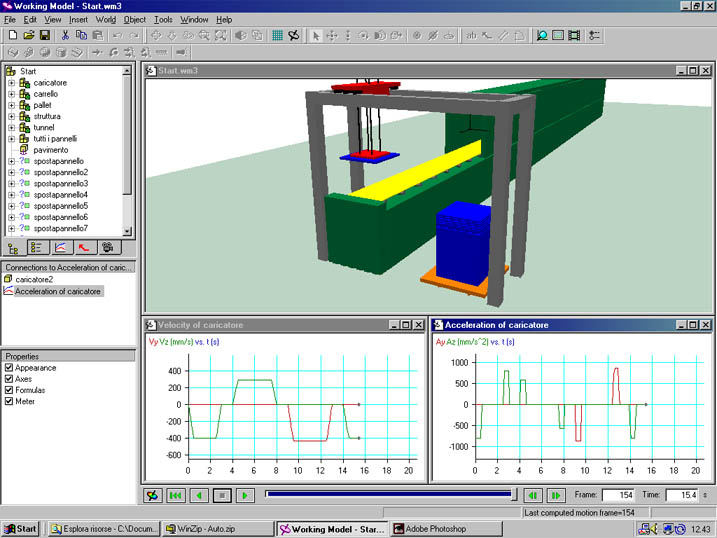
The machine moves the panels from a pile on pallet to the beginning of the production line, at a fix height. The function is realized by a pneumatic device that, once grabbed the object, lifts it up to a defined height and a trolley that moves it horizontally to the right working point where the panel is left. The complete cycle is constituted by these sequential operations:
Descent to the first panel of the pile
The pneumatic device grabs the panel
Lifting to the defined height
Horizontal sliding of the trolley till the right point
Descent to the effective working point
Leaving of the panel
Coming back to the start
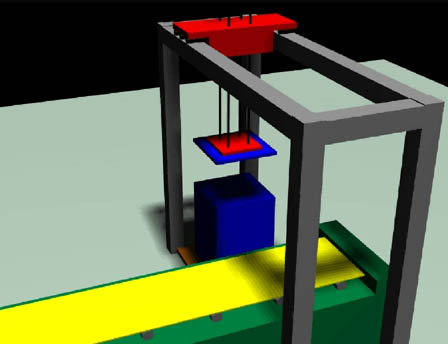
To project the control system the software used was basically MATLAB 6.0 with the extension of SIMULINK and STATEFLOW toolboxes to regulate the sequential and temporization program with the finite state machine logic (FSM): by these means, all the controlling characteristics of a PLC are reproduced to make clear any matter related to the coordination of the devices and the development of their dynamics during the correct functioning. Once obtained the optimized moving profiles of the various bodies, we proceeded to the creation of the virtual model directly with WORKING MODEL 4D and to import the data.
On the bearing structure fixed to the floor, the trolley can move horizontally with the help of a linear actuator connected to the structure itself while the grabbing device is moved vertically by a linear actuator connected to the trolley. The effect of contact with the panel is realized by a generic constraint that follows the path made by the pneumatic device.
Here it’s possible to download a reduced avi movie (1,5MB) that reproduces part of the simulation. A complete version more scenographic with audio and video effects, made by the same authors, can be requested on CD. It was used as a support to the presentation of the final work.
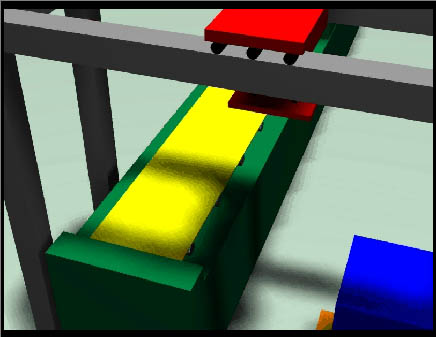
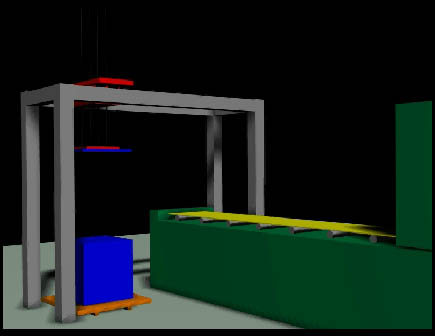
CONCLUSION
The support of a reliable model of “virtual reality” allows an optimal setting of the control strategy to obtain a remarkable improvement of the performances without modifying the instrumentation, putting down the basis to develop other new control techniques to increase the efficiency of the system, always without any change in the mechanical structure, the most expensive part of any automatized machine.
Students: Giulio Di Gravio, Francesco Costantino, Andrea Cherubini
Professor: Prof. Alessandro De Carli, Università di Roma - Italia
1,5MB movie of the virtual prototype
OTHER 83 DIFFERENT INDUSTRIAL APPLICATIONS !
ALTRI 83 CASI IN SETTORI DIVERSI !